ANSI ASSP Z9.2-2018 pdf download.Fundamentals Governing the Design and Operation of Local Exhaust Ventilation Systems
2.4 Other Recognized
Standards and Guidelines of Good Practice. ASHRAE Handbook Fundamentals. Atlanta, GA: American Society of Heating, Refrigerating and Air Conditioning Engineers ASHRAE Handbook HVAC Applications. Atlanta, GA: American Society of Heating, Refrigerating and Air Conditioning Engineers ASHRAE Guideline 1 . The HVAC Commis- sioning Process; Guideline 4, Preparation of O&M Documentation for Building Systems Although not intended for LEV systems, ASHRAE Guideline 1 provides a model of how commissioning can be performed. Heating and Cooling for Man in Industry, American Industrial Hygiene Association Industrial Ventilation: A Manual of Recom- mended Practice for Design and Industrial Ventilation: A Manual of Recommended Practice for Operation and Maintenance (two volumes), Latest Editions. Cincinnati, OH: Committee on Industrial Ventilation of the American Conference of Governmental Industrial Hygienists The 29th Edition of the ACGIH Industrial Ventilation Manual was issued in 201 6. SMACNA publications: Accepted Industry Practice for Industrial Duct Construction; Rectangular Industrial Duct Construction Standards; Round Industrial Duct Construction Standards; Guide for Steel Stack Construction; Testing, Adjusting, and Balancing HVAC Systems.
3.17 Exhaust System, LEV System. A mechanical system for removing contam- inated air from a potentially occupied space, comprised of one or more of the following elements: exhaust hood, ductwork, air cleaning equipment, exhauster or fan and stack.
3.20 Flowrate. Also, Volumetric Air Flow- rate. In U.S. units, flowrate can be specified receiving hood. The enclosing hood essentially surrounds the emission source; the capture hood is external to the emission source and relies on capturing the emission by removing the air into which the chemical contaminant is emitted; the receiving hood is a passive hood that relies on the emission and contaminated air moving into the hood by natural means. e.g., by gravity or momentum. The basic term “exhaust hood” also applies to exhaust ventilated enclosures, exhaust ventilated tools and exhaust apparatus or devices attached or integral with the process equipment when it is used, in part, for employee exposure protection. The exhaust hood normally encloses as much as possible the locations where the contaminant is released or creates air flow through the zone or zones of contaminant release of such magnitude and direction as to capture and carry the contaminated air into the exhaust system. Exhaust hoods and exhausted enclosures may also serve to keep materials within the process by preventing their dispersion.
E3.17 An LEV system operates as a functional entity and the performance of all parts is affected by the design and performance of all other parts. Although overlap may exist, an LEV system may not include some exhaust systems that directly remove process exhausts materials such as a chimney, a furnace exhaust system or other highly concentrated exhaust coming directly from a process.
E4.3 This provision will help to assure successful and reliable service. Each professional discipline should review for its own purposes: industrial hygienists may review to assure that adequate emission control will be achieved; seismic engineers, earthquake protection; fire experts, explosion and smoke controls; safety engineers, safe operating conditions; and so forth. The review should include such matters as: hood placement and enclosure, compatibility with work practices, air volume flowrates, static pressures throughout the system, transport velocities, fan pressures, stack height and locations, fire protection, potential for explosions in ductwork and air cleaners, ease of maintenance, air emissions, etc.
E4.6 The designer, working with the user, should determine proposed LEV system usage and, using appropriate dilution/ concentration prediction equations, deter- mine likely airborne contaminant concen- trations in the LEV system during various operations. Limits should be established and documented where appropriate. For example: “dilution to below one-half of the IDLH in the ductwork,” or “to below 25% of the lower explosive limit (LEL) during normal operation or worst credible accident,” etc. Such limits should be chosen by the user at the exhaust stack, in consultation with a qualified industrial hygienist or other occupational health and safety (OH&S) professional.ANSI ASSP Z9.2-2018 pdf download
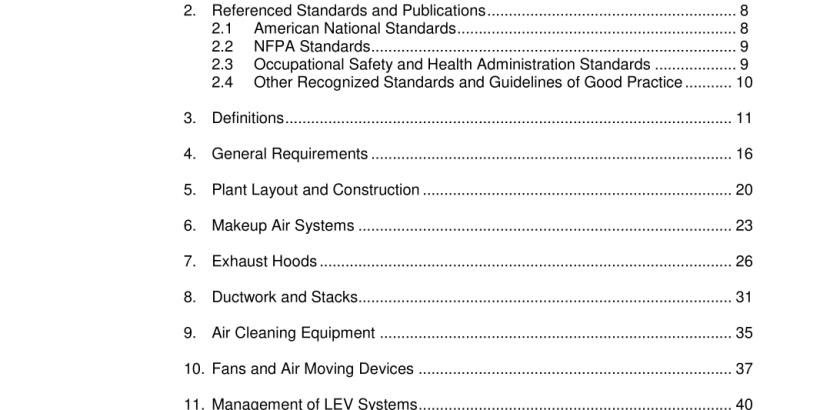