ANSI ASSP Z9.6-2018 pdf download.Exhaust Systems for Grinding, Polishing and Buffing
1.1 Scope. The requirements and emission and exposure control principles described in this standard represent the minimum criteria intended 1 ) to protect the health of personnel engaged in and working in the vicinity of grinding, polishing and buffing operations; and 2) to control contaminants generated by those operations.
1.2 Application. The standard applies to processes, equipment and operations that use power-driven machinery to grind, polish or buff a product without the use of a liquid coolant. Where liquid coolants are used, the cooling fluid may be emitted as a mist, aerosol or vapor and additional provisions will be required by the user to control exposures, pooling of liquids, draining of ducts, use of mist eliminators, and so forth, that are not covered in the standard.
1.3 Where federal, state or local regulations or codes are more stringent, those regulations and codes shall have control.
2.1 General. The regulations, codes, standards and guidelines cited in Sections 2.2, 2.3 and 2.4 contain provisions that through reference constitute provisions of this American National Standard. The related documents cited in 2.5 contain additional information, but are not essential for complying with the requirements of this standard.
3.1 Air Cleaning Equipment. A device or combination of devices for separating contaminants from the air handled by an exhaust ventilation system.
3.2 Balanced. In local exhaust systems, a balanced system is one in which the desired air flowrate is achieved simultaneously in all branches of the system.
E3.2 Balance is usually achieved through good design, proper fitting and duct selection and, when necessary, by the use of balancing dampers.
3.3 Branch Duct. A duct connecting an exhaust hood to a main or submain duct.
3.4 Commissioning, Commissioning Plan. A process or plan in which an exhaust ventilation system’s performance is identified, verified and documented before, during and after design, construction or remodeling to assure proper operation and compliance with codes, standards and user intentions.
E3.4 Commissioning ends when tests and demonstrations have verified that the system operates as intended. A commissioning agent is often used to administer the commissioning process, tailored to the needs of the system. 3.5 Contaminant. Also, Air Contaminant, Stressor. A substance (smoke, dust, fume, mist, vapor or gas) whose presence in air is harmful, hazardous or a nuisance to humans.
3.11 Disc Wheel. All power-driven, rotating discs faced with abrasive materials, artificial or natural, and used for grinding or polishing on the side of the assembled disc.
3.12 Document; to Document; Documentation. The formal process of planning and recording of the rationale for decisions made by the user, the designer or others. Also, the written procedures devel- oped for operating, testing and maintaining an LEV system.
3.13 Ductwork. Elongated rigid or flexible enclosures used to convey air and entrained contaminants from one location to another.
3.14 Entry. The point at which a segment of ductwork (i.e., branch or submain) enters another segment of ductwork (i.e., submain or main); entry from a hood to a duct; and entry from a plenum to a duct.
E7.1 After an exhaust system is installed, it should be tested initially and periodically to assure that it performs according to design or operating performance criteria, normally established before installation and during the commissioning process. Performance criteria (e.g. “the flowrate should be 1,000 scfm; the hood static pressure should be 0.75” w.g.,) are useful because testing and measurements can confirm satisfactory performance. Exhaust system components to be tested usually include the hood or exhausted tool or enclosure, the air cleaner and the fan. Performance criteria should usually include such parameters as: hood static pressure; minimum air volume flowrate; average; minimum, and maximum hood face velocities; visual containment; measured containment performance factors; capture velocity; slot velocity; transport velocity; pressure drop across air cleaners; fan total pressure; motor amperage; and so forth, as appropriate.ANSI ASSP Z9.6-2018 pdf download
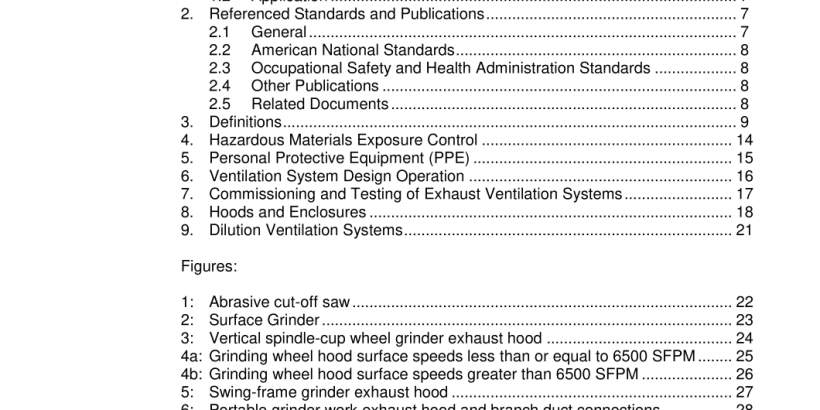