CSA ANSI Z21.93-2017 pdf download.Excess flow valves for natural gas and propane gas with pressures up to 5 psig
3 Definitions The following definitions shall apply in this Standard: Body — The principal structure of a device that contains and supports an actuating mechanism and constitutes the main gas passage. BTU — Abbreviation for British Thermal Unit. The quantity of heat required to raise the temperature of 1 pound of water 1°F. Excess flow valve, (EFV) — A device installed in a fuel gas piping system to automatically trip when the rate of passage of fuel gas through the device exceeds a predetermined level (trip flow). Excess flow valve bypass, (EFVB) — An excess flow valve designed to limit the flow of fuel gas after trip of the excess flow valve to a predetermined level and to reset automatically after the pressure is equalized across the valve. Excess flow valve non-bypass, (EFVNB) — An excess flow valve designed to stop the flow of fuel gas after trip of the excess flow valve and to be reset manually. Bypass flow — An internal rate of passage of fuel gas through an bypass excess flow valve after trip of the bypass excess flow valve, which will allow upstream and downstream pressure to equalize across the device to automatically reset to the open position. Liquefied petroleum gases — The terms “Liquefied Petroleum Gases,” “LPG” and “LP-Gas” as used in this standard means and includes any material that is composed predominantly of any of the following hydrocarbons, or mixtures of them; propane, propylene, butanes (normal butanes or isobutane), and butylenes. Maximum flow capacity — The highest rate of passage of fuel gas through an excess flow valve specified by the manufacturer that allows for normal operation of the appliance(s) the excess flow valve serves. This shall not be more than 90 percent of rated trip flow. Orifice — The opening in a cap, spud, or other device whereby the flow of gas is limited and through which the gas is discharged to the burner. Rated trip flow — The minimum trip value as specified by the manufacturer that will cause the excess flow valve to stop of limit the flow of fuel gas.
5.3.2 Turning effort
A valve shall be capable of withstanding, without deformation impairing valve operation, breakage or leakage, the turning effort shown in Table 3 exerted by assembling to piping or tubing. The construction of a sectional valve body shall be such that when the turning effort specified in Table 3 is applied across the body parts in any direction that would act to disassemble the valve, the valve body sections shall not start to separate. The following Method of Test shall not apply to valves having flange connections. Method of Test This test shall be conducted at an ambient temperature of 77°F ± 10°F (25 °C ± 5.5 °C). A wrench of suitable size shall be used to apply the turning force. SAE 10 viscosity machine oil shall be applied to the taper threads of steel pipe nipples, which shall be inserted in the inlet and outlet of the valve and turned up hand tight. With the inlet nipple secured in a vise, the specified turning effort shall be applied to the outlet nipple. For other than straight through type valves, the tests shall be repeated as outlined above except with the outlet nipple inserted in the vise and the turning effort applied to the inlet nipple. Valves designed for tubing connections shall be tested as outlined above except that the torque shall be applied at opposite ends of the valve body through wrench flats or bosses and not to the tubing fittings. There shall be no evidence of deformation, breakage, or impairment of operation as a result of making up inlet and outlet connections. After relaxation of the applied torque, the valve shall comply with the provisions of Clause 5.4.CSA ANSI Z21.93-2017 pdf download
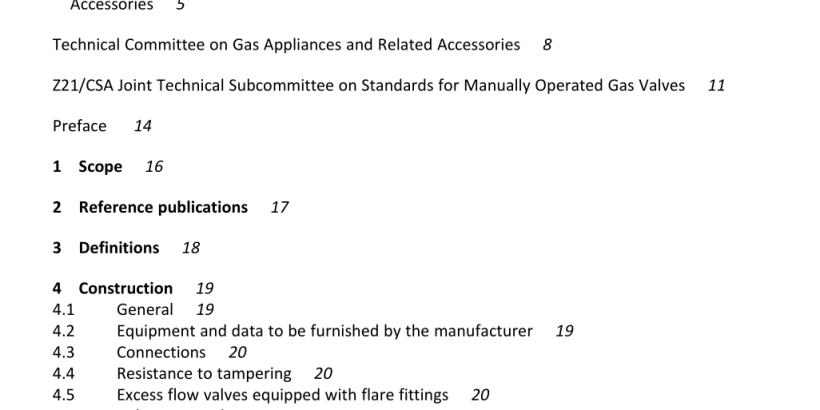