ANSI B109.2-2000 pdf download.DIAPHRAGM-TYPE GAS DISPLACEMENT METERS
3.2.1.1 Test Conditions.
a. Beil prover operating on air at a minimum of 1.5 inches water column (375 Pa) gauge.
b. Differential Pressure Gauge. A precision manometer accurate to 0.01 inch water column (2.5 Pa) gauge, and equipped with a snubber to dampen pulsations to a maximum of 0.02 inch water column (5 Pa).
c. Test System Piping. The piping of the pressure tap assemblies shall be Schedule 40 pipe of the same nominal size as the meter connections. Pressure tap assemblies shall be as shown in Figure 5. The pressure tap holes shall not be less than 118 inch (3 mm) nor more than 114 inch (6 mm) in diameter and shall be drilled perpendicularly to the wall, and the center line of the hole shall intersect the center line of the pipe. The intersection of the pressure hole and the inside surface of the pressure tap assembly shall be free from burrs and preferably slightly rounded. No pressure tap connection shall be used that distorts the inside surface of the pressure tap assembly or that projects into the passage.
d. To determine the capacity, the meter on test shall comply with the accuracy specifications of 3.3.1. The connection sizes for meters on qualification test are as indicated in 2.2.1, Tables I and II.
3.2.1.2 Meter Class Test. With the meter connected to the test system and the bell prover supplying test air, the control valve shall be adjusted until exactly 0.5 inch water column (125 Pa) differential is read on the differential pressure gauge (any small fluctuations should be averaged into the reading). With a stopwatch, the bell shall be timed for a unit volume displacement as indicated by the prover xale to determine the observed air flow rate through the meter. The proving bell temperature and the barometric pressure shall be noted at the time of the test.
Pilot flow accuracy can be-determined as described above for the operating flows or by the use of a calibrated orifice having the required Bow rate connected to the meter outlet and the air or gas supplied at constant pressure. Timing of a registered volume through the meter and comparing this flow rate with the calibrated onfice’s flow rate shall determine the pilot flow accuracy. Prior to initiation of accuracy tests, meter and piping system shall be tested for tightness and all leaks eliminated.
3 3 3 Accelerated Life Test.
To determine the ability of a displacement meter to measure gas accurately for relatively long service periods, ii shall be subjected to an accelerated life test. To comply with this provision, the meter shall continue to operate and register for the entire period of the accelerated test. NOTE: After the accelerated life test, the meter shall be tested and shall comply with the sustained accuracy specifications of 3.3.2. Method of Test Meters shail be leak- and flow-tested and calibrated before being placed on the test rack. Meters shaü be calibrated to an accuracy of 100 Io.296 in accordance with 7.5.5.4. Meters shall be installed on a test rack, using the type of gas for which the meter is intended. Flow rate through meters shall be maintained between 180% and 22û% of rated capacity. After total meter index registration is equal to 8.ooO times the 0.5 inch water column (125 Pa) or 4,000 times the 2.0 inches water column (SOO Pa) rated hourly capacity, the accuracy of the meter shail be within the limits specified in 3.3.2.
3.5.1 Each new-type meter shall be tested to establish that it is able to withstand an internal pressure in excess of that to which it may be subjected in actual service. A shell (or case) pressure test shall be performed on all meters to a minimum pressure of 10 psig or at 1 .5 times the MAOP, whichever is grealer, for cast steel, cast aluminum and wrought aluminum shells, and at 2.0 times MAOP for cast and ductile iron shel]s. (Reference Section VIll, ASME Boiler and Pressure Vessel . Code).
3.5.2 Each new-type meter shall be given a pressure leak test while submerged in water, or a 1est equivalent in sensitivity, to determine that it is free from leakage. During the test, the me1er shall be slowly pressurized [not exceeding 5 psi per second (34 kPa)] with a gas, from 0 psig 10 at least 1.25 times the MAOP.ANSI B109.2-2000 pdf download
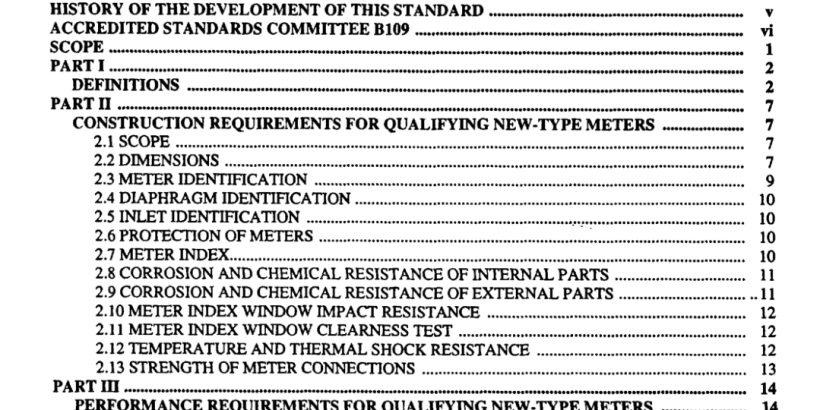